Applying zinc finishing to small metal components, such as fasteners, screws, and switch plates, enhance the components’ corrosion resistance. Zinc is a bluish-white metal commonly applied to iron, brass, and other alloys via one of two methods—zinc plating or zinc flake coating—each of which carries its own unique advantages and use cases.
The following provides an overview of the two methods, outlining their basic processes, benefits, and typical applications.
Zinc Plating: Overview
Zinc plating—also referred to as galvanization—employs an electrical current to facilitate the application of a thin coat of zinc to the surface of a metal component.
The zinc oxidizes, creating a protective layer of zinc oxide that prevents the base metal from being exposed to the surrounding environment. It is largely used for iron or steel parts that would otherwise rust when exposed to air or water.
Benefits of Zinc Plating
In addition to corrosion resistance, steel and iron plated with zinc demonstrate several advantages over their non-plated counterparts, such as:
- Higher strength
- Easier formability
- Lighter material weight
- Greater recyclability
- Superior cost-effectiveness
Applications of Zinc Plating
Zinc plated components find application throughout
industries in indoor and mildly corrosive environments. Typical parts that undergo the zinc plating process include:
- For automotive industry: steering transmission parts and brake calipers
- For hardware industry: brackets and fasteners
- For military industry: Underbody and suspension components, weapon systems, arms and accessories
For components subjected to more corrosive environments, industry professionals may add a chromate-conversion coating for greater corrosion resistance.
View Zinc Plating
Zinc Flake Coating: Overview
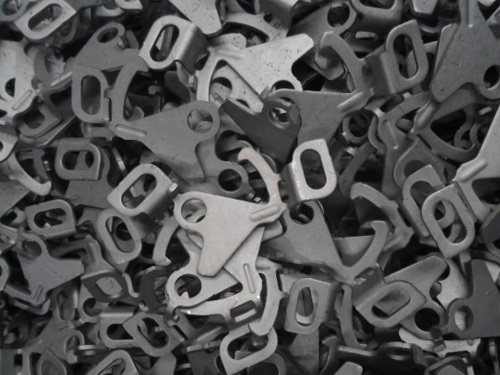
During the design of everything from mechanical assemblies to buildings, corrosion protection is a key consideration. Even the smallest components, such as nuts and bolts, must be adequately protected from corrosion. Otherwise, they risk compromising the integrity of the entire system or structure.
Zinc flake coating is an ideal solution for these applications. These coatings typically contain a mix of zinc and aluminum flakes and are applied in two layers—a base coat and a top coat—the characteristics of which combine together to satisfy the requirements of the application. When a zinc flake coated part is exposed to a corrosive compound, the zinc sacrifices itself to protect the base metal.
Zinc Flake Coating Benefits
Beyond protecting iron, steel, and other metals from corrosion due to atmospheric compounds, salt spray, and mild chemicals, zinc flake coatings offer many other benefits, such as:
- Fewer corrosion byproducts, or white rust, than other types of zinc protection
- Broader versatility for parts of different shapes, sizes, and geometries with options for varying layer thicknesses and colors
- Better protection against hydrogen embrittlement
- Some electrical conductivity
- Greater wear and extreme temperature resistance
View Zinc Flake Coating
Applications for Zinc Flake Coating
Zinc flake coatings are applied to a variety of parts and system components used in a diverse set of industrial applications, including:
- For automotive industry: Automotive sub-frames, chassis assemblies, fasteners, springs
- For MEP industry: Construction building components
- For commercial/recreational applications: Home appliances
- For industrial/manufacturing applications: Threaded fasteners, small integrated components such as bolts, nuts, pressings, springs, and clips
- For utilities and energy industry: Wind energy generators
Zinc Finishing Solutions from Pioneer Metal Finishing
At Pioneer Metal Finishing, we offer the highest quality zinc plating and zinc coating services. For more information on our zinc-related products and services, or assistance choosing the method best suited for your application,
contact us today.
Contact Us