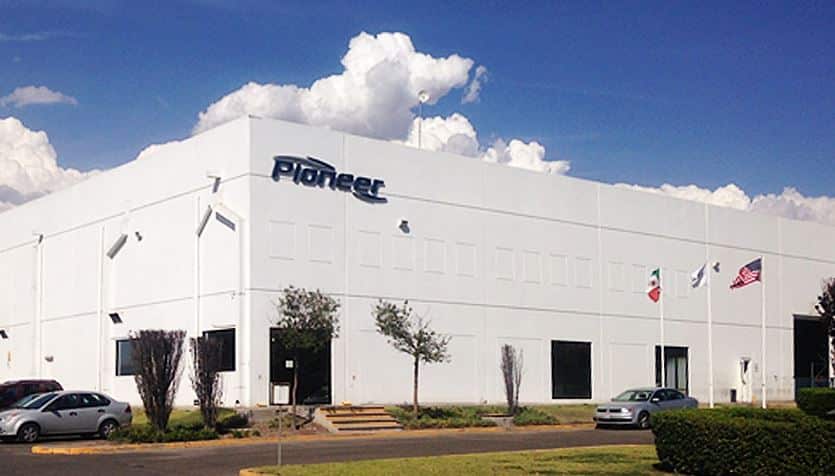
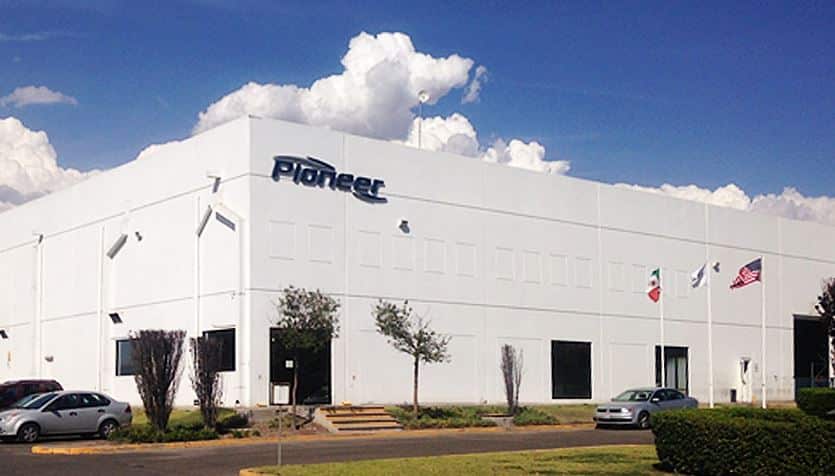
By Andrew Schunk
Rubber & Plastics News Staff
GREEN BAY, Wis.—For 75 years, Pioneer Metal Finishing quite literally has had the metal and plastics industries covered, through its unique rubber and polyurethane finishing, coating, plating and anodizing expertise across a range of markets.
The company began in 1945 in Minneapolis with a focus on functional applications, just as it continues today, according to Troy Oscar, automotive market leader for Pioneer. Through various acquisitions over the years and the addition of rubber-to-metal bonding capabilities in 2012, Pioneer has grown into a global company with nine manufacturing locations and more than 1,000 employees.
“Our company DNA has been strongly centered around applications that require a high degree of precision and quality control,” Oscar said. These are precisely the qualities that are needed in the medical and aerospace fields for surgical instrument coatings and optical and navigation equipment.
But Pioneer’s services have proved equally important in the automotive, agriculture, housewares, industrial, outdoor recreation, paper, print and packaging industries, according to Pioneer.
Now privately owned by New York-based Aterian Investment Partners, the global company with manufacturing facilities in the Midwest, West Coast and Mexico has 1 million square feet of total production space across those locations. Pioneer can place its coatings and adhesives onto aluminum alloys, aluminum casting, aluminum forging, copper, plastic, rubber, stainless steel, steel and zinc die casting.
“Over our 75-year history, Pioneer has grown through strong organic expansion of business as well as strategically acquired new businesses that provide additional value to our portfolio,” Oscar said.
The company’s growth is focused on three areas: geographic coverage, technology expansion and industry offerings. Pioneer supports each manufacturing location through a “strong but nimble” corporate structure that Oscar said is focused on engineering, quality and corporate shared services.
“The ability to leverage our locations, along with a central engineering group, has made us a leader in the industry,” Oscar said. “Pioneer would like to be known as a thought leader and solution provider. Our goal is for our customers to come to us to help them solve the most challenging surface engineering problems.”
Perhaps despite the coronavirus outbreak, Pioneer’s strongest material markets continue to be in anodizing (a conversion coating process used to achieve an oxidized surface finish on metals for corrosion and wear resistance), industrial plating and coatings operations.
Pioneer said its coatings and finishings also allow for improved lubricity, or friction reduction; conductivity; dielectric insulation; solder ability; heat dissipation; infrared signature reduction; and either high or low reflectivity.
And the technologies that have come with the onset of autonomous and electric automobiles has not gone ignored by Pioneer, either.
“As the automotive industry continues to expand on the use of lightweight materials, aluminum finishing is in high demand,” Oscar said. “Additionally, our coatings business continues to be in high demand.”
In the rubber-to-metal realm, Pioneer can apply adhesives, which help bond rubber to metal for suspension and mount customers. Pioneer has noted “quite a lot of movement in the automotive space” because of the evolving technology needs, Oscar said.
“The need for lighter weight, longer life and non-internal combustion engine vehicles is driving our customers to push the boundaries of traditional surface engineering applications,” he said.
In the rubber-to-metal bonding process, Pioneer prepares a component substrate for bonding by mechanical or chemical pretreatment, Oscar said, adding that Pioneer’s pretreatment and primer/adhesive processes are an integral part of obtaining a strong bond.
Pioneer offers zinc and manganese phosphate pretreatment coatings, as well as complete parts washing and blasting services to prepare the substrates for the critical application of adhesives.
The adhesives and coatings, mainly provided by Lord Corp., Dow Chemicals Co. and H.B. Fuller Adhesive Manufacturing Co.’s Cilbond brand, can be applied using chain-on-edge spray systems, dip spin and dip drains. Lower volume methods such as hand spray also are offered.
Following the pretreatment, a primer and adhesive are applied to the metal or plastic component. These components are shipped to customers, where the components are inserted into a mold. A heated liquid form of rubber is then injected into the hot mold, curing it to the plastic or metal component.
Specific end uses for rubber-to-metal (or plastic) bonding include bushings, mounts and exhaust isolators.
“All these NVH parts are used to reduce noise, vibration and harshness in the vehicle so the passenger enjoys a more comfortable ride,” Oscar said.
Bouncing back from pandemic
During the coronavirus pandemic, Pioneer has been considered an essential industry by the U.S. government. While the company’s automotive plants were significantly impacted by OEM shutdowns, causing some downtime, Pioneer is now fully operational once again. “We are back up and running,” Oscar said.
Pioneer responded to a call to assist the front lines during the pandemic as well, working extensively with several of the ventilator/automotive manufacturing partnerships.
“Our experiences in both the automotive and medical device space have helped us to support this critical work over the last several months,” Oscar said. “We are proud of this work and the overall contributions being made in this critical effort.”
As Pioneer looks ahead to future technology and market temperaments for some of the most cutting-edge industries in the world, Oscar said some new innovations are on the horizon.
“Our customers are seeing some very interesting technology evolutions occurring, using lighter weight materials such as aluminum and titanium in the aerospace and defense spaces to conserve fuel or energy,” he said.
The ability to provide corrosion protection and durability for these materials also is critical in high-altitude, harsh environments. “From a coatings standpoint, the ability to prepare and apply primer and adhesives to these new materials is critical as well,” the Pioneer executive said. “We’re seeing significant increases in the use of plastic and the ability to prepare the surface. A strong bond is critical for our customers.”
Academy stirs new thinking
Such technologies should advance even further under Pioneer’s relatively new Surface Engineering Academy, an online platform that features best practices and industry processes.
The forum, available through the company’s website, offers expert-level surface engineering and operational resources through webinars, expert panel sessions, white papers, how-to handbooks, technical articles and technology development resources.
“We are very excited to launch Surface Engineering Academy as part of our ongoing efforts to help our customers optimize the performance of their products,” said Pioneer CEO Kevin Stevick. “Given the complexity, breadth and development of surface modification options, our goal is to create a technically focused venue that helps to drive continuous improvement in this important category. Pioneer is thrilled to support this new and important resource.”
Oscar said the academy is designed to further customer education, which hopefully leads to advancements not only for Pioneer, but for the overall metal and plastics finishings industry.
“As thought leaders in the industry, we want to partner with our customers to help them determine the best solutions for their products,” Oscar said. “As our customers become more educated with finishing, plating and coating, the more we can collaborate on the development of new solutions.”
While not a new category, the use of legacy technologies—such as anodizing, plating, adhesives and coatings—continues to represent an important evolution in the finishings industry. This, coupled with the use of “thin film disposition” and new surface modification technologies, has significantly expanded the options for solving tribological (interacting surfaces in relative motion), adhesive application and corrosion protection challenges, among others.
“SEA, at its core, is designed by our operations and product development teams,” said Scott Kettler, chief operating officer of Pioneer. “It offers a peer-to-peer, technologist-to-technologist platform to further surface technology development, increase operational efficiencies and share insights and industry best practices.
“The surface modification space offers great potential for improving the performance of mission-critical products. We are excited to be a part of these important development efforts.”
Reprinted with permission from Rubber & Plastics News. © 2020 Crain Communications Inc. All rights reserved.
Further duplication without permission is prohibited. RPN19001